|
 |
In some cases a manifold originally intended for a different engine may be adapter or modified. Some will require spacers under the intake port flange either to adapt the bolt pattern, add height for a taller deck, or both. The height of the intake port in the flange will vary somewhat between engines, so this also changes placement.
The number, size and position of manifold bolts is not critical. If the original holes aren’t useful but are too close to ignore, it’s easier to thread the hole and insert a piece of threaded aluminum bar stock, then tig only the top and bottom (instead of welding the hole completely) - less distortion. When in doubt, spot-face the upper flange surface parallel to the correct flange angle so you can add a thick washer to spread the load over the flange (especially if the bolt is large vs. the flange width, or near the flange edge). If not practical, use spherical washers to align the underside of the bolt to the (incorrect of unfinished) flange angle.
The manifold flange angle (where it meets the head) will vary between brands and even between engines in the same brand. This affects gasket seal if the difference is more than a few degrees (which can generally be made up in gasket crush). A manifold spacer can also adapt the flange angle somewhat, but the math to do this is not as simple as it appears. If the manifold widths are too close for a spacer, generally it is preferable to modify the manifold (making the angle on the head different may be easier to do, especially if the head is being machined for another purpose like compression - saves set-up time), but this means it can’t take the stock manifold any more.
Making the flange angle more vertical (taking material from the outer edge of the flange) makes the manifold narrower, making the flange more horizontal (taking material from the inner edge of the flange) does not - remember to include this in your width calculations.
In many cases, the “make or break” decision is based on whether the donor engine matches the project as to having a separate valley cover (Chrysler hemi, Olds, Chrysler B/RB etc.) or integral valley covers (SBC, BBC, Chrysler LA, etc.). Engines with separate valley covers are easier to adapt.
Except under extremely unusual circumstances where the transition between the manifold flange and the head port will be several inches long, the port layouts must match. The donor manifold must have the correct size and shape intake port, or slightly smaller. In no instance may the manifold port overlap the head flange, but must have free flow into the intake port at all points although it may be somewhat smaller.
The bore pitch (the center-to-center distance between adjacent cylinders in the same bank) must be similar. Gross differences will cause a fatal mis-alignment on three of the four ports in each bank.
There is no fixed maximum bore pitch difference that an adaptation will tolerate, since thicker walled castings, large pitch distances and large port areas obviously can ”hide” a larger error.
The preferred method is to center the inner cylinder pairs (3 & 5 and 4 & 6) of the manifold on the heads. This “averages out” the difference in bore pitch, so that the alignment error of each of the paired inner cylinders is ½ of the bore pitch difference.
An example: if the manifold’s bore pitch is 4.800” (Chrysler B) and the Buick 430 heads are 4.750” the difference is .050”; let’s call this the “pitch error”. The 3 & 5 and 4 & 6 inner cylinders will be off by .025” from ideal. The outer cylinders will inherit this error, and add their own pitch error of .050” for a total of .075” each for cylinders 1, 2, 7, & 8.
This is preferable to perfect alignment at one end, where each successive cylinder is cumulatively worse. Not only is the maximum error much greater, but the range of mis-alignment between all cylinders is much greater: 0-.150” or .150”, compared to .025”-.075” or .050”, making for potential mixture bias problems: |
Cylinder pair | Preferred “centered” method | “From one end” method |
1, 2 | .075” pitch error | .000” pitch error |
3, 4 | .025” pitch error | .050” pitch error |
5, 6 | .025” pitch error | .100” pitch error |
7, 8 | .075” pitch error | .150” pitch error |
For a manifold comparison, subtract the pitch distance from any engine in the Table below from the pitch distance of your subject engine (doesn’t matter if the result is a negative number). The outer four cylinders (1, 2, 7, 8) will mis-align by 1.5 × the pitch error, and the center four cylinders (3, 4, 5, 6) will mis-align by .5 × the pitch error.
Here is a table of the most common automotive V6 and V8 engines, ranked by bore pitch, along with their intake port configuration.
V6 & V8 Bore center distances |
Engine | Size | Pitch | Ports |
Ford modular OHC | 4.6, 5.4 | 3.937” | 00 00 |
Lexus “UZ” | | 4.154” | 0 0 0 0 |
Dodge hemi & poly | 241, 259, 270, 315, 325 | 4.1875” | 0 0 0 0 |
| 3.8 | 4.193” | 0 00 |
Buick, Chevrolet, Olds, Pontiac V6 | 198, 225, 231, 252 | 4.24” | 0 00 |
Buick, Rover, Olds, Pontiac V8 | 215 | 0 00 0 |
Buick V8 | 300, 340, 350 | 00 00 |
| 2.0, 2.5, 3.0, 3.5, 3.8 | 4.252” | 0 0 0 |
DeSoto hemi | 276, 291, 330, 341, 345 | 4.3125” | 0 0 0 0 |
| 239, 256, 272, 292, 312 | 4.38” | [] [] [] [] |
Ford 335 (W, C, M, B) | 221, 260, 289, 302, 351, 400 | 0 0 0 0 |
Chevrolet SB | 265, 283, 302, 307, 327, 350, 400 | 4.40” | 00 00 |
Chrysler poly A | 277, 301, 303, 313, 318, 326 | 4.46” | 0 0 0 0 |
Chrysler LA | 273, 318, 340, 360 | 00 00 |
Studebaker | 224, 233, 259, 289, 304.5 | 4.50” | 00 00 |
Cadillac *-1966 | 331, 365, 390, 429 | 4.5625” | 00 00 |
Chrysler hemi & poly | 301, 331, 354, 392 | 4.5625” | 0 0 0 0 |
Pontiac | 287, 326, 347, 350, 370, 389, 400, 421, 428, 455 | 4.62” | 00 00 |
Olds Rocket | 303, 324, 371, 394 | 4.625” | 00 00 |
Oldmobile | 330, 350, 400, 425, 455 | 0 0 0 0 |
Lincoln & truck Y-block | 279, 302, 317, 332, 341, 368 | 4.63” | 00 00 |
Ford FE | 332, 352, 360, 390, 401, 410, 427, 428 | 0 0 0 0 |
Rambler *-1965 | 250, 287, 327 | 4.75” | 00 00 |
AMC 1966-* | 290, 304, 343, 360, 390, 401 | 00 00 |
Buick nailhead | 264, 322, 364, 401, 425 | 4.75” | 0 00 0 |
Buick | 400, 430, 455 | 00 00 |
Chrysler B/RB | 350, 361, 383, 413, 426, 440 | 4.80” | 00 00 |
Chrysler RB hemi | 426 | 0 0 0 0 |
Chevrolet W | 348, 409, 427 | 4.84” | 00 00 |
Chevrolet BB | 366, 396, 402, 427, 454 | 00 00 |
Ford MEL | 383, 410, 430, 462 | 4.90” | 0 0 0 0 |
Ford 385 | 332, 352, 360, 390, 401, 410, 427, 428 |
Cadillac 1967-* | 368, 425, 472, 500 | 5.00” | 00 00 |
Packard | 320, 352, 374 | 5.125” | 00 00 |
Water flow (if any) must be examined carefully. In some cases, the manifold is the only transfer between banks and must be retained. Water can generally be plumbed separately with external lines; they can even be made attractive with chrome or brass tubing.
A completely fabricated (“custom”) manifold is very expensive. Using an existing aluminum manifold just for the flanges, last 2” of the runners, plenum body, valley cover, water passages etc. saves a huge amount of work.
Cut a big box out of the top, and graft on something similar to what you want - get the donor from a similar engine on eBay with some corrosion, broken ears, pulled studs etc. Obviously, the port layout should match what you have for best effect and least re-designing.
You can (if you wish) assemble it with studs and nuts for testing before final welding - it only needs to hold 15 psi vacuum. Allows dividers, porting, radiusing etc. not possible with a casting.
Click here to read about constructing a traditional “old-school” log manifold: |
Adapting a manifold to a 4 cylinder or 6 cylinder inline (L-4, L-6) is a similar process, except that the deck height and width of the engines is not relevant. The same requirements as to bore pitch, bolt pattern, port alignment &c. must be met.
L4 & L6 Bore center distances |
Engine | Size | Pitch | Ports |
AMC | 199, 232, 4.0L, 258, 4.6L | 4.38 | |
Chevrolet Gen-2 | 216, 235, 261 | Alternately 4.1875”-4.375”-4.1875”, &c. | O O O |
Chevrolet Gen-3 | 194, 215, 230, 250, 292 | 4.40” | 0 [ ] [ ] 0 |
G.M.C. | 228, 236, 248, 256, 270, 302 | Larger between cylinders #2-3 and 4-5 than between cylinders #1-2, 3-4 and 5-6, perhaps 4.375” and 4.5625”? | O O O |
|
|
See these Victory Library booklets |

|
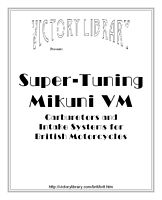
|
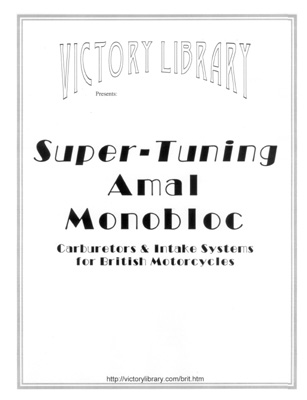
|
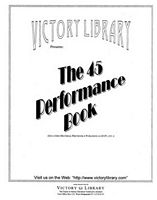
|
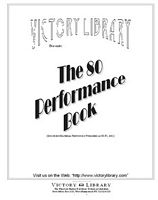
|
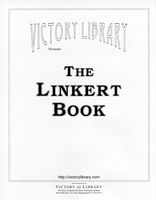
|
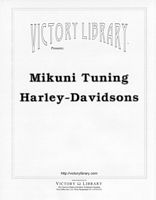
|
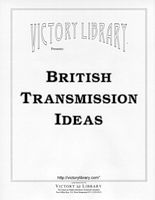
|
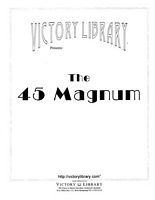
|
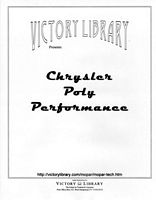
|
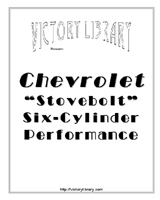
|
GMC, supercharger, blower, 6-71, 671, 8-71, 871, pressure, adapt, convert, manifold
|